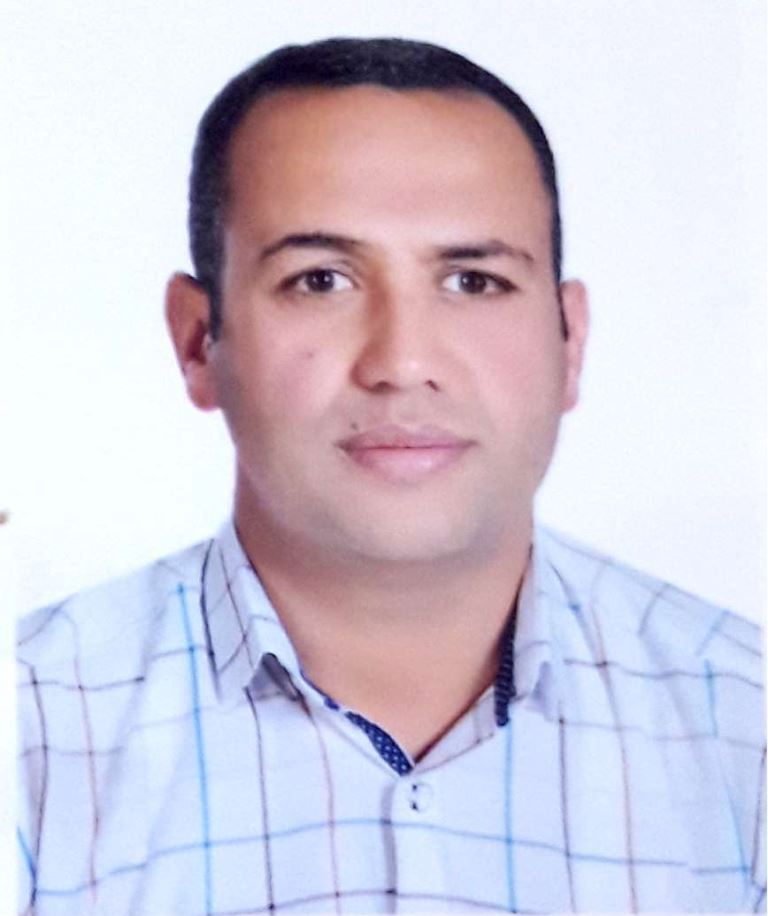
Omer Khalil Ahmed
Research InterestsRenewable energy
Power engineering
Heat transfer
Gender | MALE |
---|---|
Place of Work | Hawija Technical Institute |
Position | Dean of Institute |
Qualification | Ph.d |
Speciality | Renewable energy |
dr.omer.k.ahmed@ntu.edu.iq | |
Phone | 07708080836 |
Address | Iraq-Kirkuk-hawija, Kirkuk, Mosul, Iraq |
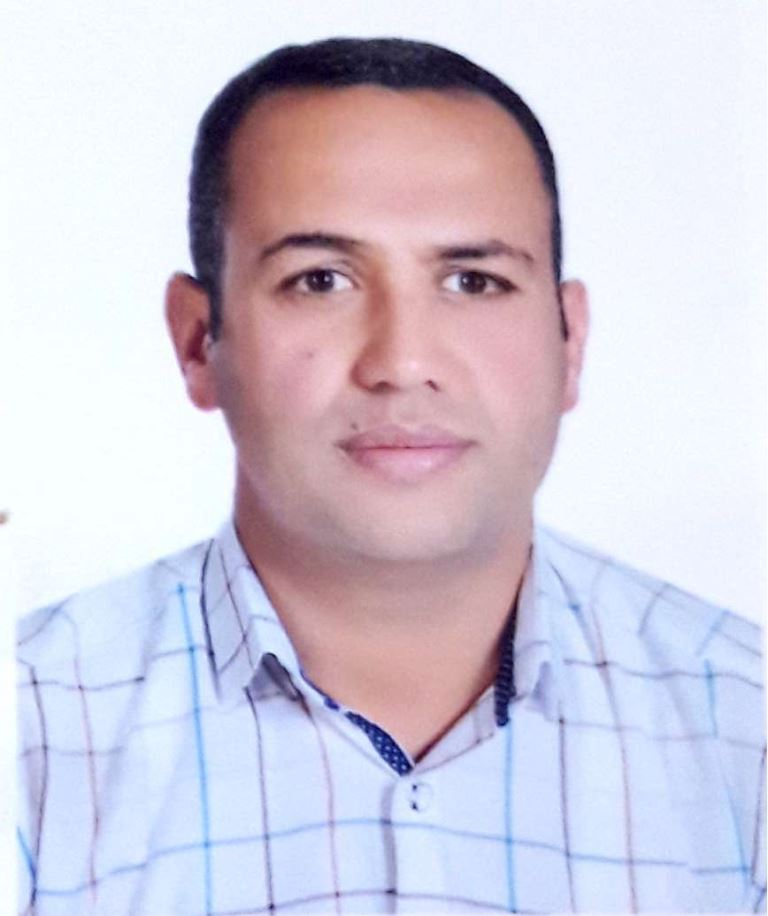
Dr. Omer Khalil Ahmed obtained a Bachelor's degree in Mechanical Engineering. He was the first in the Faculty of Engineering at the University of Tikrit - Iraq in 1999. He received a master's degree in Energy Engineering and Generation Sciences from the same university in 2001. Dr. Omer Khalil Ahmed obtained his Doctor of Philosophy degree in Mechanical Engineering (Renewable Energy Engineering) in 2006 from Al-Nahrain University, Iraq. He also served as Head of the Department of Mechanical Technologies and the Renewable Energy Research Unit and supervised many doctoral and master's students. He has published numerous technical papers in reputable journals and international conferences in the fields of renewable energy, internal combustion engines, energy efficiency, power systems, and thermal science.
Academic Qualification
PhD (Renewable energy)
Sep 5, 2002 - May 7, 2006Al-Nuhrain university, College of enginneing
MSc. Eng. (Power generation)
Oct 5, 1999 - Nov 27, 2001Tikrit university- College of engineering
Bachelor of Mechanical Engineering (Hon.)
Oct 1, 1995 - Jul 1, 1999Tikrit University, Iraq
Working Experience
Kirkuk [Assisstance lecturer- Technical college/Kirkuk]
Aug 5, 2002 - May 7, 2006Publications
Performance assessment of water vortex power plant: Effect of material type and blade number
Apr 12, 2025Journal Results in Engineering
publisher Elsevier
DOI https://doi.org/10.1016/j.rineng.2025.104775
Issue June 2025, 104775
Volume Volume 26
This article aims to evaluate the performance of water vortex power plants by studying the effect of turbine material type, number of blades, and height to enhance the efficiency of sustainable energy generation using turbine systems. The research used an experimental model to simulate an operating environment similar to turbine power plants. The experiment included the use of turbines made of carbon alloys and galvanized alloys, with variable numbers of blades (four blades and six blades) and different heights from the bottom of the basin (1.5 cm, 3 cm, 5 cm, and 8 cm). The rotation rates and resulting force were measured on both sides of the turbine, and the system efficiency was calculated using accurate measuring tools to ensure the reliability of the results. The results showed that the type of turbine material, number of blades, and turbine height directly affect the performance. For example, a turbine made of carbon alloy with four blades and a height of 3 cm achieved a rotation speed of 89 rpm, a generated force of 15.67 N, and an efficiency of 68.6 %. In contrast, the six-blade turbine under the same conditions showed a higher rotation speed of 100 rpm, but the efficiency dropped to 64 %. These results highlight that increasing the number of blades can enhance the rotation speed but may decrease efficiency, reflecting the importance of balancing design and function to achieve optimal performance.
Performance Augumation of PV/Solar Chimney Using Gravel Bed: Experimental Appraisal
Mar 4, 2025Journal Energy storage
publisher Journal of Thermal Engineering
DOI https://doi.org/10.1002/est2.70149
Issue Issue2
Volume Volume7
This study aims to analyze and enhance the performance of a solar/voltage chimney by incorporating porous media, specifically using a gravel layer beneath the solar panels to facilitate cooling and improve efficiency. The gravel acts as a heat transfer medium, dissipating heat from the panels to the surrounding air, thereby reducing their temperature. A comparative analysis was conducted between systems with and without porous media. The results demonstrated that integrating porous media enhances the performance of the hybrid photovoltaic/solar chimney. Specifically, the electrical energy output increased from 395.56 W without porous media to 447.98 W with porous media at noon. The peak electrical efficiency was observed at the beginning of the test, reaching 14.51% without porous media and 15.22% with porous media at 9 a.m. At midday, electrical efficiency was 11.5% without porous media and 12.2% with porous media. However, as solar radiation intensity increased, efficiency gradually declined. On the other hand, the thermal efficiency of the chimney with porous media was lower compared to the system without it, with values of 53.45% and 59.611%, respectively. The total efficiency of the system without porous media was 65%, while with porous media, it reached 59.611%.
Effect of the design variables on the vortex water turbine performance
Mar 1, 2025Journal Journal of Thermal Engineering
publisher Journal of Thermal Engineering
Issue No. 2, pp. 314−330, March, 2025
Volume Vol. 11
The water vortex power plant has become of more interest to researchers due to its important role in renewable energy technologies, allowing it to operate with low heads and flow rates. The novelty of the work compared to previous efforts is that a group of variables studied together that have an important role in increasing the efficiency of the system, such as the increase and decrease in the number of blades, the effect of weight through changing the type of metal, and the height of the turbine from the bottom of the basin. Therefore, this article evaluated the performance of the water vortex plant, in which several variables were studied: the number of turbine blades, turbine weight, and turbine height from the basin floor where the water vortex system was designed and tested by using four turbines: one of them had six blades and another four blade are made from carbon steel alloy and two other turbines, which one of them six blades the other four blades are made of galvanized alloy. Practical tests also concluded that the four-blade turbine, made of carbon steel alloy, achieved an efficiency of up to 69%. The weight of the turbine plays a vital role in determining the system efficiency when a six-blade turbine made of carbon alloy with a higher weight and a height of 3 cm reaches 64% as the maximum efficiency. Also, the experiments found that the highest efficiency reaches the turbine at a height of 3 cm from the bottom of the basin after different heights were chosen for the turbines used from the bottom, which included (1.5 cm, 3 cm, 5 cm, 8 cm).