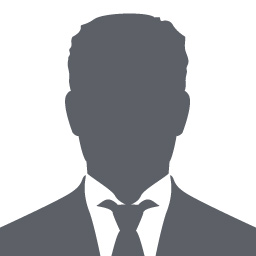
Zina Saad Abdul Jabbar
Research InterestsMetallurgy
metal forming
composite materials
3D printers
Gender | FEMALE |
---|---|
Place of Work | Technical Engineering College/ Mosul |
Position | مسؤولة وحدة الارشاد |
Qualification | Master |
Speciality | Mechanical engineering |
zena.saad@ntu.edu.iq | |
Phone | 00 |
Address | Mosul, 00, Mosul, Iraq |
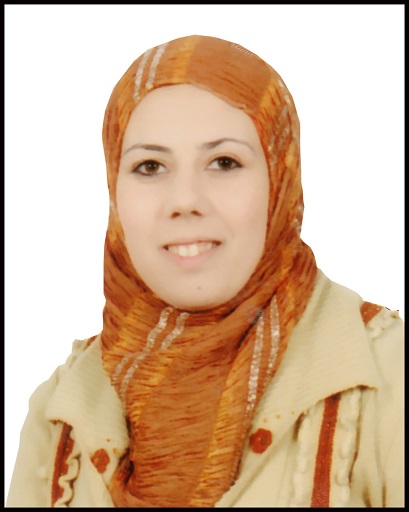
Name: Zina Saad Abdul Jabbar
Education:
• B.Sc. in Mechanical Engineering – University of Mosul, 2007
• M.Sc. in Mechanical Engineering – College of Engineering, 2023
Current Position:
• Lecturer at the Technical Engineering College
• Head of the Student Guidance Unit at the Technical Engineering College
Academic Experience:
• Teaching advanced engineering subjects for fourth-year students
• Teaching engineering subjects for second-year students
• Teaching Practical Strength of Materials for second-year students
• Teaching in the Departments of Power Mechanics Techniques and Applied Mechanical Engineering
Skills:
• Proficient in theoretical and practical mechanical engineering fields
• Strong academic teaching and course preparation abilities
• Excellent student guidance and mentoring skills
Languages:
• Arabic (native)
• English (good in comprehension and academic writing)
Publications
Experimental Investigation of the Effect of Die Shape on Mechanical Properties of Aluminum Alloy by Hot Direct Extrusion Process
May 9, 2024Journal International Journal of Mechanical Engineering and Robotics
DOI 10.18178/ijmerr.13.3.331-337
Issue 2024
Volume 13
Abstract—This experimental study examined the impact of die shape on the mechanical characteristics of the AA7075, the aluminum alloy, extruded by hot direct extrusion. These characteristics include the extrusion load, hardness and compression tests, and stress-strain curve. Three alternative widths of the extruded metal exit zone (16, 18, and 20 mm) and three different die angles (15°, 30°, and 45°) were considered in the experiments. According to the findings, the extrusion load for the extruded items was the highest at an angle of 30° and the lowest at an angle of 15°. In terms of the hardness test of extruded materials specimens, the hardest areas were located at the outer circumference for all extrusion diameters and angles. Although the extruded samples’ compression test results showed variations in the samples’ loads before and after extrusion, it was also noticed that some of the other samples’ stress and strain curves converged while others had only slight differences.