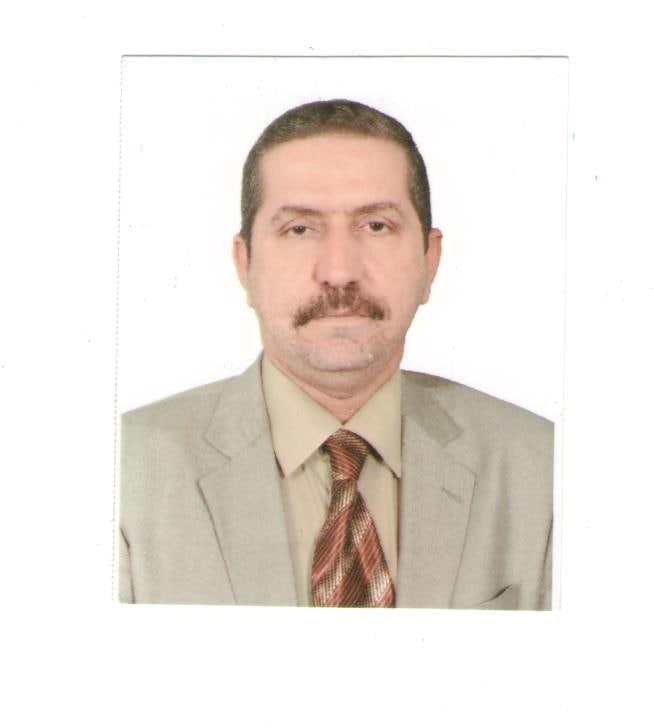
Salah F. Abduljabbar
Research InterestsFatigue
Biomechanics
Kinesiology
Gender | MALE |
---|---|
Place of Work | College of Health & Medical Techniques / Al-Dour |
Position | Library Division Officer |
Qualification | Ph.d |
Speciality | Applied mechanic |
salah.fa@ntu.edu.iq | |
Phone | 07707960473 |
Address | aldour, salahdin, al-dour, Iraq |

Skills
ANSYS WORKBENCH (80%)
Academic Qualification
Bacheloris
Sep 1, 1986 - Jun 30, 1990MSc
Oct 1, 2003 - Jul 1, 2005Applied Mechanics
PHD
Sep 1, 2008 - Oct 25, 2012Applied Mechanics
Publications
The effects of Heat Treatment (T6) Technique and some Centrifugal Casting Parameters on the Fatigue behavior of the Composite Material (A380/Al2O3)
Sep 30, 2017Journal Tikrit Journal of Engineering Sciences
DOI http://dx.doi.org/10.25130/tjes.24.3.05
Volume 24
Aluminum alloys composite is one of the most common types of composite materials that are widely used in the recent years. This paper deals with the effects of the heat treatment techniques and some centrifugal casting parameters on the fatigue behavior of the composite material (A380/ Al2O3) for high-cycle fatigue resistance which is one of the most important properties for the automotive industry. Aluminum alloy A380 is used with alumina particles Al2O3 to form a composite material through the process of centrifugal casting. The proportions are 10% and 20% with a grain size 63μm. Then, thirty-two models of composite material (A380/Al2O3) have been manufactured. Half of them are examined directly without treatment while the other half was treated with (T6) and then examined. The results showed that adding the amount of alumina 20% without heat treatment will increase relatively resistant composite material for the fatigue resistance by 17% percentage. Adding 10% alumina to the composite material causes distortion of the surface structure samples which marked by blisters and are completely discolored. A high Alumina content improves the fatigue behavior of the composite material (A380/ Al2O3).
Study of the Effect of Al2o3&B4c Particles Reinforcement on Some Physical and Mechanical Properties for Aluminum Alloy 6063 by Powder Metallurgy Technique
Sep 3, 2019Journal Diyala Journal of Engineering Sciences
DOI http://dx.doi.org/10.24237/djes.2019.12305
Volume 12
Powder metallurgy technique utilized in samples preparing. Samples were compacted by using cold uniaxial pressing then followed by sintering process at 600 oC under inert gas. Results showed improving in (Brinell Hardness, wear resistance & compression strength) and increasing in (density, porosity & water absorption). Brinell Hardness increasing (106. – 114.7), compression strength increasing (35.1 – 40.8) N/mm2 and decrease wear rate (6.6*exp(-8) – 4.22*exp(-8)) g/cm at time 30 min. with (0 – 20)% Al2O3&B4C. While increase apparent density (2.76 – 2.83) g/cm3, Bulk Density increase (2.71-2.82) g/cm3 apparent porosity decrease (1.88 – 0.193) % and water absorption decrease (0.699 – 0.068) % at (0 – 20) % Al2O3&B4C.
Mechanical and Wear Behavior of Al7075 - Graphite Self-Lubricating Composite Reinforced by Nano-WO3 Particles
Apr 17, 2020Journal Materials Science Forum
DOI https://doi.org/10.4028/www.scientific.net/MSF.1002.151
Volume 1002
Al7075 hybrid nanocomposites considered one of the most material utilized in modern engineering applications that required a combination of superior properties such as lightweight, high strength, excellent corrosion resistance, and high thermal conductivity. In the current study, Al7075 – 5 vol % graphite self-lubricating composite was reinforced by 0, 1.5, 2.5, 3.5, and 4.5 vol % WO3 nanoparticles in order to study the microstructural, mechanical, and wear characteristics. The classical powder metallurgy route was employed to fabricate the hybrid nanocomposites specimens. The microstructural analysis of the nanocomposites was characterized by utilizing a Field Emission Scanning Electron Microscope (FESEM) and Energy-Dispersive X-ray (EDX) analyses. Mechanical properties such as micro-hardness and diametral compressive strength were studied. Dry sliding wear test was performed under the various loads of 10, 15, 20, and 25 N at a sliding distance and sliding speed of 1810 m and 1.5 m/s, respectively. Results have revealed that the microhardness and diametral compressive strength considerably improved by increasing the WO3 content until 3.5 vol % and then slightly decreased. Besides, both the values of the wear rate and friction coefficient gradually reduced by increment the reinforcement content up to 3.5 vol % and then suddenly increases for all the applied loads. Nevertheless, the wear rate and friction coefficient were correlated positively with the applied loads. From the results obtained, graphite as solid lubricating material with WO3 nanoparticles was successfully combined into the Al7075 alloy matrix. The optimum mechanical and wear performance of the hybrid nanocomposite were revealed at 3.5 vol % content of WO3 nanoparticles.